In the production process of a product, if in a new batch, the amount of MFI varies uncontrollably and unconsciously, it can have destructive effects on the productivity and quality of the product. Therefore, it is very important that the materials entering the production unit are tested with the relevant standards and their accuracy is confirmed.
test method
The sample can be in the form of granules, powder, film strips or slices of the product so that it has the ability to enter the machine.
First, depending on the approximate MFI of the sample, you should take 3 to 8 grams of the sample. The 5g value of the prototype is suitable for all MFI values.
Turn on the device and put it in the test temperature. Depending on the type of material, this temperature is included in the technical specifications or product characteristic standard. However, in the table below you can see the temperature and weight of the MFI test for some common plastics.
When the device reaches the desired temperature, you should wait about 15 minutes for the stabilization to be done and also clean the cylinder of the device with a suitable cloth. Cleaning cloths can be suitable for this task.
After this time, pour 5 grams of the sample you weighed into the cylinder and compress the material by hand. Make sure the filling is as air-free as possible. The filling process should be done in less than 1 minute. Immediately after that, wait 5 minutes for the ingredients to preheat.
After this time, place the piston inside the cylinder and place the appropriate test weight on the piston. Like the temperature, this weight depends on the type of material and it is mentioned in the above table.
There are 2 marks on the piston that determine the test interval. Materials start to leave the die by melting and under the force of weight. When the first mark line of the piston reaches the upper part of the device while going down, it is the right time to start sampling. Maximum sampling can continue until the second mark line of the piston reaches the upper edge of the device. During this period, you can cut and separate the outputs of the die during certain periods of time. For example, for an approximate MFI between 0.1 and 0.15, the appropriate cutting time is 2 minutes. Or for MFI between 0.15 and 0.4, this time can be 1 minute etc.
You should separate at least 3 of these slices and weigh them. The average mass obtained is the mass of the sample that was removed from the machine in the molten state during the test period (cutting time). Calculate the amount of mass output from the device in 10 minutes or the same value of MFI with the closing ratio.
Important points in taking the MFI test
- All the samples you cut and weigh should be free of any bubbles and unmelted spots.
- The mass difference of different cuts should not be more than 15%.
- The minimum number of slices should be 3.
- The length of each cut should be between 10 and 20 mm.
When the test is performed in accordance with the Iranian National Standard No. 6980-1, the mass flow rate of the melt of the raw materials, the polymer layer of the pipe and also their difference should be in accordance with Table 9.
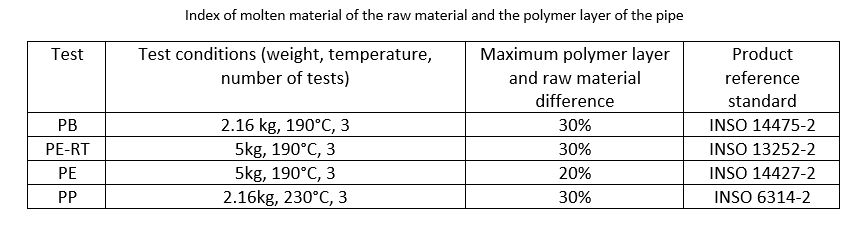